BuildYourCNC
CNC Standalone Controller (No Computer Needed)
CNC Standalone Controller (No Computer Needed)
Affiliate Links
Description: DDCSV3.1
Price: $245.00 USD
See ProductDescription: DDCSV4.1 500KHz
Price: $359.00 USD
See ProductDescription: DDCS Expert 1000KHz
Price: $365.00 USD
See ProductDescription: 1000KHz DDCS Expert with MPG Handwheel
Price: $450.00 USD
See Product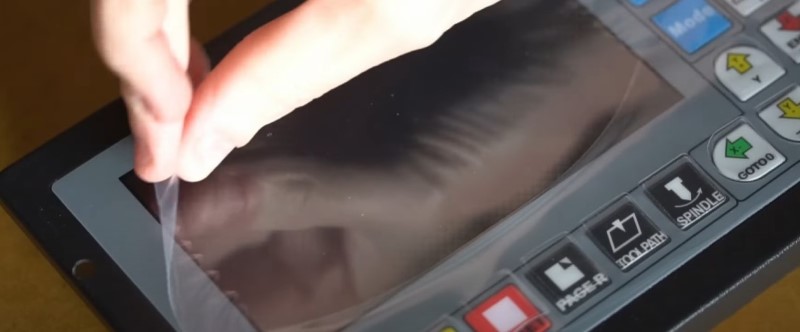
Share


Questions & Answers
Have a Question?
-
What post processor do you recommend for this controller with Vcarve Pro?
The most generic post processor should be used with this controller.
-
The description for this stand alone 3.1 controller describes the pendant as being included, but when you link to the Amazon site for this item, the MPG pendant is not included int the $250 price.
Thanks. I updated that option to reflect that it has no pendant.
-
Is a closed loop system possible with the DDCS Expert?
You can connect closed-loop motors and drivers to this controller. The feedback loop is only between the driver and the motor. When the controller commands the motor to reach a specified location, the motor/driver combination will attempt to get to that position, but if unable to reach the position, the driver will output an error signal which can be wired to the controller to stop the machine. As with all closed-loop drivers and motors, if you stop the movement, and then allow the movement to continue, it will reach it's intended destination since the driver receives the encoder values from the motor. Most controllers work this way and the DDCS is no exception.
-
I plan to use a DDCS stand alone controller for a CNC router build which will have two stepper motors on the x axis, one on Y and one on Z. Will the 3.1 version handle two motors synched on the X axis or will I need the 4.1 version?
No, the 3.1 version will not support slaving the X axis. You will either need to wire the two x axis driver to the same X signal pins, or use the DDCS v4.1 which does support slaving an axis.
-
Do you know how to connect a second Probe for tool lenght and Relais for Air pressure ?
Yes, I can configure a system that contains a relay and solenoid to control air pressure and adding a second probe for tool height.